Injection moulding is one of the most widely used manufacturing processes for producing plastic parts at scale. However, to get the most out of it, your design must be compatible with both the behaviour of plastic materials and the technical limitations of the tooling and moulding process.
Designing a part that looks good in CAD isn’t enough. If your design doesn’t account for how molten plastic flows, cools, and shrinks, you risk production issues that are costly, time-consuming, and difficult to fix once tooling is built.
At AC Plastics, we help customers avoid these common pitfalls with upfront design reviews and technical guidance. Below are ten mistakes we often see, along with explanations of why they matter and how to get it right the first time.
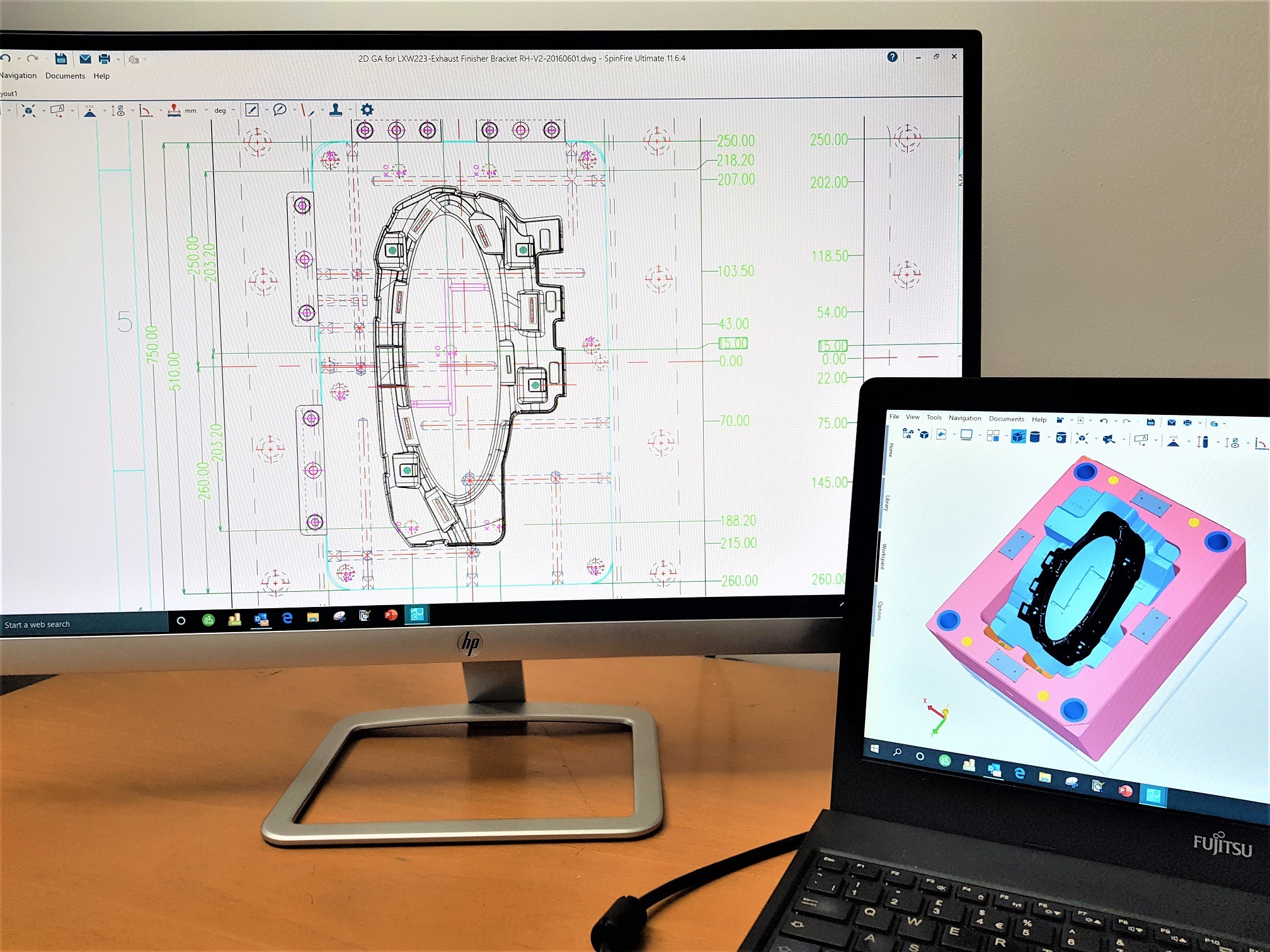
1. Inconsistent Wall Thickness
Why this causes problems:
When plastic flows into a mould, it begins cooling and solidifying from the outer surfaces inward. If the wall thickness varies too much across the part, the cooling rate becomes inconsistent. Thicker sections retain heat longer and shrink more as they cool. This leads to internal stress, warping, and cosmetic defects such as sink marks. It can also prolong cycle times and reduce dimensional stability.
How to avoid it:
Aim for uniform wall thickness across the part. Where variation is unavoidable, transition gradually between different thicknesses to minimise stress concentration.
How AC Plastics helps:
We assess CAD designs for problematic thickness variations and advise how to maintain flow and cooling consistency. Our feedback reduces scrap and improves mouldability.
2. Lack of Draft Angles
Why this causes problems:
Draft angles allow the part to release from the mould without dragging, sticking, or damaging the tool. Without them, ejection forces increase, which can cause part distortion, surface scuffing, or premature wear of the mould. In the worst cases, the part may become stuck, halting production.
How to avoid it:
Add draft angles (typically 1–2 degrees) on all vertical faces, increasing for textured surfaces. Apply greater draft where parts have deeper draw depths or high-friction finishes.
How AC Plastics helps:
We flag insufficient draft during design reviews and suggest modifications to ensure clean ejection, reduced wear on tooling, and longer production uptime.
3. Poor Material Flow Design
Why this causes problems:
Plastic must flow smoothly through the mould cavity to avoid short shots, weld lines, air traps, and inconsistent filling. Sudden direction changes, long flow paths, thin sections, or poor gate placement can all interrupt flow. This leads to defects, weak points, or visual blemishes.
How to avoid it:
Design parts with gentle curves, balanced wall thickness, and logical flow paths. Position gates to promote symmetrical filling and reduce flow lengths where possible.
How AC Plastics helps:
We run mould flow simulations to predict flow behaviour and advise changes before tooling. This allows issues to be resolved early, avoiding expensive corrections later.
4. Incorrect Rib Design
Why this causes problems:
Ribs improve structural stiffness, but if they’re too thick or positioned poorly, they cause sink marks, longer cooling times, and increased material use. Thick ribs cool at different rates than adjacent walls, leading to cosmetic dips on visible surfaces.
How to avoid it:
Keep rib thickness to around 50–60% of the wall it supports. Add fillets at the base of ribs to ease material flow and prevent sharp transitions.
How AC Plastics helps:
We help optimise rib geometry to maintain strength without sacrificing surface quality. This keeps tooling simple and improves cycle efficiency.
5. Sharp Internal Corners
Why this causes problems:
Sharp corners increase stress concentration, which makes parts more prone to cracking or mechanical failure. They also hinder plastic flow, resulting in incomplete filling, air entrapment, or poor surface finish. From a tooling perspective, sharp internal corners are harder to machine and can wear faster.
How to avoid it:
Use radii or fillets on internal corners, particularly where two surfaces meet at right angles. Rounded corners reduce stress and promote better material flow.
How AC Plastics helps:
We recommend corner radii that balance part strength and mouldability, helping ensure your design supports both function and efficient production.
6. Not Accounting for Material Shrinkage
Why this causes problems:
All plastics shrink as they cool, and each material has a specific shrinkage rate. If this isn’t factored into the tool design, parts may come out undersized, distorted, or dimensionally inconsistent – especially across thicker areas.
How to avoid it:
Use accurate shrinkage values for the selected material and incorporate them into your design and tool drawings. Consider direction-dependent shrinkage, especially for semi-crystalline polymers.
How AC Plastics helps:
We use material-specific shrinkage data based on years of production experience. Our tooling suppliers work from adjusted dimensions to ensure the finished part meets exact tolerances.
7. Overly Complex or Tool-Unfriendly Features
Why this causes problems:
Complex features such as deep undercuts, enclosed voids, or internal threads require additional tooling elements like side actions or lifters. These features increase tooling cost, lead times, and maintenance requirements, and may introduce more failure points.
How to avoid it:
Design for simplicity. Avoid undercuts unless essential and consider whether complex features can be redesigned, separated into multiple parts, or added post-moulding.
How AC Plastics helps:
We identify features that will complicate tooling and suggest practical alternatives, helping you keep costs under control and lead times realistic.
8. Inadequate Venting
Why this causes problems:
As plastic flows through a mould, it displaces air. If that air has nowhere to go, it becomes trapped, causing burn marks, voids, or incomplete filling. Poor venting is especially problematic in thin-walled parts or at the end of fill areas.
How to avoid it:
Ensure that part geometry allows air to escape, and that tooling includes proper vent channels at strategic points.
How AC Plastics helps:
We work with toolmakers to review and implement effective venting strategies, reducing the risk of defects caused by trapped gases or pressure build-up.
9. Over-Specifying Tolerances
Why this causes problems:
Overly tight tolerances increase tool complexity and lead to higher manufacturing and inspection costs. Injection moulding inherently includes some dimensional variation, and trying to hold precision where it isn’t needed results in unnecessary scrap or rework.
How to avoid it:
Apply tight tolerances only to features that require them. Use standard tolerances for cosmetic or non-critical areas.
How AC Plastics helps:
We advise where tolerances can be relaxed without affecting performance, balancing quality with practicality to ensure economical and reliable production.
10. Skipping Prototyping or Design Validation
Why this causes problems:
Skipping prototyping risks going straight to production with a flawed design. Once tooling is built, changes can be time-consuming and costly. A design that looks good in CAD may fail in real-world testing due to assembly issues, mechanical weakness, or fit problems.
How to avoid it:
Use prototyping methods such as 3D printing, soft tooling, or CNC-machined parts to evaluate function and assembly before final tooling.
How AC Plastics helps:
We offer a range of prototyping options to help validate your design, ensuring smoother transitions into full production and reducing the risk of costly errors.
Partner with AC Plastics for Smarter Design and Reliable Production
Design mistakes in injection moulding cost time and money. But with the right advice early in the process, they can be avoided. Whether you need help selecting materials, improving part geometry, or validating your design before tooling, AC Plastics can support you every step of the way.
We offer a complete design-to-manufacture service including CAD support, mould flow analysis, toolmaking, moulding, assembly, and more. Based in the UK and trusted across multiple sectors, we combine decades of hands-on experience with modern manufacturing capability.
Ready to get your design right first time?
Contact AC Plastics today to speak to our engineering team about your next injection moulding project.