Injection moulding is one of the most popular manufacturing methods for creating plastic components. It’s widely used across industries like automotive, medical, and packaging because it’s efficient, cost-effective, and capable of producing highly detailed parts. But how does the injection moulding process work? This guide will walk you through the key steps, from initial concept to the final product, so you can better understand how it all comes together.
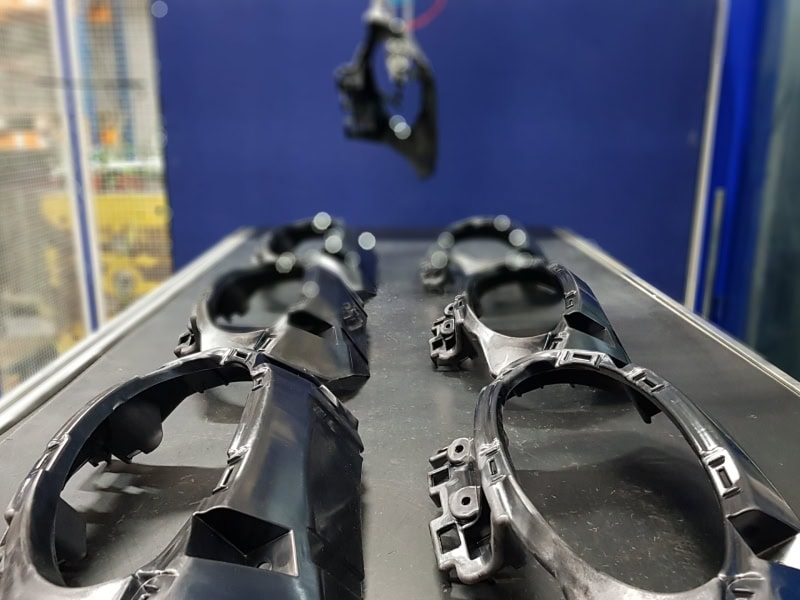
What is Injection Moulding?
Injection moulding is a manufacturing process where plastic is melted and injected under pressure into a mould to create a specific shape. Once cooled and solidified, the finished part is ejected from the mould tool, and the cycle begins again. This process is ideal for mass production, offering precision and consistency across thousands—or even millions—of components.
Why Choose Injection Moulding?
Injection moulding stands out for several reasons:
- Scalability: Perfect for high-volume production.
- Flexibility: Compatible with various polymers and complex designs.
- Efficiency: Once set up, the process runs quickly, keeping costs per unit low.
- Quality: Produces durable, detailed parts with minimal post-processing.
Key Steps in the Injection Moulding Process
Let’s break down the process step by step:
Step 1: Designing the Product and Mould
Before production begins, the design stage is crucial. Engineers create a mould tailored to the product’s specifications. Prototypes may be tested using 3D printing or CAD simulations to ensure everything works perfectly. Choosing the right polymer for the job is also vital, as different plastics offer various characteristics, such as durability, flexibility, or temperature resistance.
Step 2: Feeding and Melting the Material
Raw plastic, typically in the form of granules or pellets, is fed into a hopper at the top of the injection moulding machine. These granules are then heated in a cylindrical barrel, where a screw rotates to melt the plastic evenly, using friction (known as shear) as well as heat from external heating elements. Maintaining the correct temperature is critical to prevent scorching or uneven flow of the plastic material through the barrel and into the mould.
Step 3: Injecting the Molten Plastic into the Mould
Once melted, the plastic is injected into the mould under high pressure. The mould consists of two halves, one fixed and one moving open and closed between cycles. The mould cavity is the hollow centre between the halves, and its shape and profile determines the area in which the molten plastic can flow, forming the shape of the plastic product. The mould also contains a core, which is of varying complexity and is used to form the internal product features. Precise control over the injection speed and pressure of the molten plastic ensures the mould is filled properly without defects like short shots, flash or warping.
Step 4: Cooling and Solidifying the Part
After injection, the plastic begins to cool and solidify within the mould. This step can take seconds or minutes, depending on the material and the part’s complexity and thickness. Cooling channels within the mould help maintain the right temperature, speeding up the process and making the mould cycle more efficient.
Step 5: Ejecting and Finishing the Product
Once the part has cooled, ejector pins or plates push it out of the mould. Automation can also be used to remove finished products using a robotic arm, or 3-axis robot. The product is then inspected for quality before being packaged, or sent for further processing. Occasionally, finishing touches like polishing or removing excess plastic (called sprues or runners) are required to achieve the desired appearance, or parts are painted or coated in secondary processes for aesthetic or functional improvements.
What Makes Injection Moulding So Effective?
- High Volume Production: Injection moulding is designed for efficiency. Once the mould is created, the process can churn out thousands or millions of identical parts in a short time, meaning an incredibly economical price per part in high volume production.
- Precision and Consistency: The tightly controlled parameters of injection moulding ensure every part meets exact specifications, reducing waste and rework, and creating vast amounts of identical components.
- Versatility in Design and Material: From small, intricate components to large, durable parts, injection moulding can handle a wide range of designs. It’s also compatible with various plastics, including recyclable materials, or blends containing recycled content. A wide variety of additives and masterbatches can also be added during the moulding cycle, giving new properties or colouring the mouldings uniformly, during the same process.
Common Challenges in Injection Moulding
While injection moulding is highly efficient, it’s not without challenges. Common issues include:
- Material and Design Considerations: Selecting the wrong plastic, poor mould design or non-optimised process parameters can lead to defects like warping or incomplete parts. Experienced moulding companies will be well versed in these considerations and optimise materials, tooling and process variables for best results.
- Quality Control Issues: Problems like blistering, short shots, and burn marks can occur if temperature, pressure, or cooling times aren’t carefully managed. Experienced moulding technicians will alleviate these issues and optimise moulding parameters to alleviate defects, and quality control after the moulding process ensures no sub-standard parts are delivered.
- Economics: Injection moulding is incredibly cost efficient when manufacturing thousands or millions of parts. However, the up-front cost of a mould tool means that lower volumes will be more expensive per part. Experienced moulders or toolmaking companies will help plan out the process based on production volumes, and alternatives such as aluminium tooling instead of hardened steel tools may be more suitable and cost effective for low volumes.
Routine maintenance of injection moulding machines and quality inspections during production can help address these challenges, as well as working with a reputable moulding company, whose experienced technicians will be well versed in process optimisation.
Modern Innovations in Injection Moulding
The injection moulding industry is constantly evolving, with exciting innovations that improve efficiency and sustainability:
- Smart Technologies and Industry 4.0: Manufacturers now use data analytics and automation to monitor and control every stage of the process, ensuring consistent results. With interconnected machinery, equipment and ancillaries, moulders have more data than ever before, allowing for greater optimisation and synchronisation of all equipment and parts of the process. This reduces waste, increases productivity and minimises energy consumption.
- Sustainability and Recycled Materials: Advances in polymer science and equipment allow the easier use of recycled plastics, reducing environmental impact without compromising quality. Mouldings regularly incorporate a percentage of recycled materials, allowing the reuse of existing materials and a lowering of a product’s carbon footprint.
- Electric Machinery: Electric injection moulding machines are replacing traditional hydraulic models, offering energy savings and greater precision.
Conclusion: From Concept to Completion
Injection moulding is a highly efficient and versatile process, capable of bringing complex ideas to life. From designing the mould to producing consistent, high-quality parts, every stage is carefully controlled to ensure the best results. With its ability to handle large volumes, precise designs, and a variety of materials, injection moulding remains a cornerstone of modern manufacturing.
Whether you’re developing a new product or exploring better production methods, understanding the injection moulding process is the first step towards making informed decisions.
Let Us Help You Make It Happen
Whether you need help with designing your mould, selecting the right materials, or finding the ideal injection moulding supplier, we’re here to help. Get in touch today to learn more about how injection moulding can work for you. Let’s make your concept a reality!